The Importance of Pressurisation and Air Management in Closed Systems
Imagine yourself assembling IKEA furniture. After putting it all together, you notice that there is one screw left unused and you have no idea where it goes! You put it wherever you can. That is the story of our industry’s attitude towards pressurisation units and air management in chilled water systems.
Water being an incompressible medium, expands as temperature increases and contracts when temperature decreases. When temperatures rise, system media expands, pressure builds up and the subsequent strain on individual components eventually leads to rupture and failure. When temperatures fall, the volume reduces and the fall in pressure leads to air intake that causes corrosion, cavitation, noise and pitting — the biggest enemies of HVAC installations.
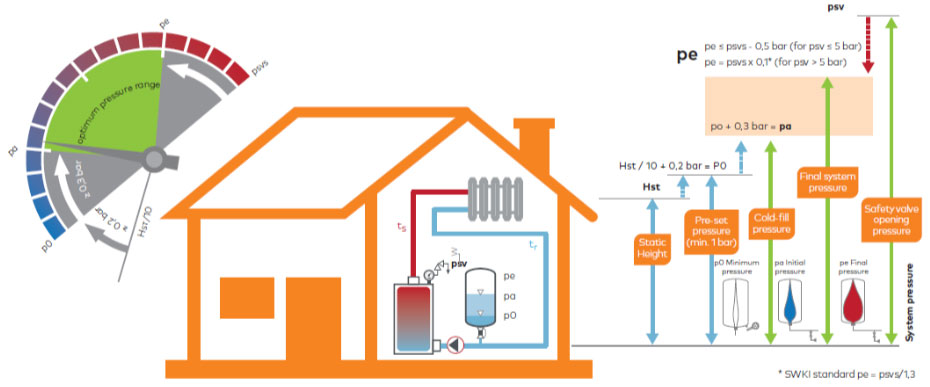
*Source: IMI Pneumatex: Breakthrough Engineering
Given the above, we see that a wrong selection and/or sizing of pressure maintenance systems can severely damage components such as pumps, control valves and coils, which in turn, undermine the performance and life expectancy of the system.
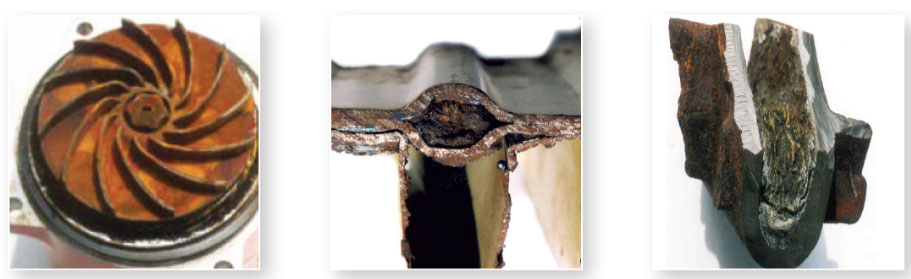
Examples of system damage linded to water quality issues
There are numerous causes of air in a system such as:
- The amount of air dissolved in the water of the water make-up system.
- Air trapped in the system after the initial fill.
- Diffusion.
- Air ingress due to negative pressure.
Examining Make-up Water Systems:
Apart from system negative pressure, the biggest source of air in closed systems is the water make-up system. In the vast majority of cases, in the case of conventional pressure maintenance systems, expansion vessels are typically heavily undersized. This is largely due to a lack of knowledge on the designer/installer’s part about the impact of pressure factor “Pf” on the efficiency of the expansion vessel and suppliers taking advantage of this. This results in almost the entire burden of pressure maintenance being carried by the water make-up system!
But what gases constitute the air in such systems? Detailed below are the gases dissolved in make-up water at the molecular level of 14.3 ml/l N2 and 7.8 ml/l O2.
Oxygen: Several studies have shown that, despite chemical dosing, O 2 in the make-up water is completely used up by the initial corrosion process within 4-5 hours. (As seen in the yellow line in the graph.)
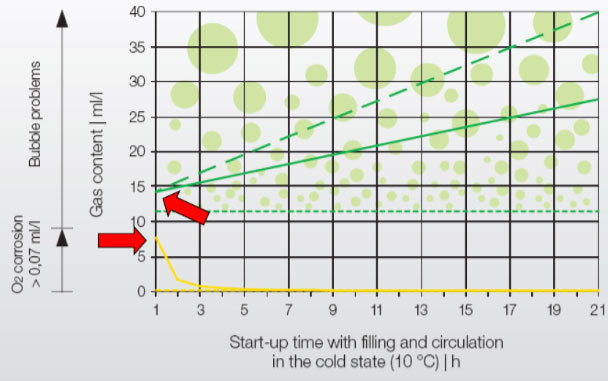
*Source: IMI Pneumatex: Breakthrough Engineering
Calculation:
3Fe + 2O2 → Fe3 O4 (Magnetite rust)
(4✕16) mg O2 → (3✕56) + (4✕16) = 232 mg Fe3 O4
1 mg O2 → 3.6 mg Fe3 O4
1 Litre Make-up water = 7.8 ml O2 → 11.42 mg O2 → 40mg Fe3 O4
1 m 3 of Make-up water → 40g Fe3 O4
This is not a negligible amount of rust!
Nitrogen: If one believes nitrogen is an inert bystander, think again! Due to the unique ability of the N2 molecule to flex, the behaviour of nitrogen varies with pressure as shown below as per Henry’s law.
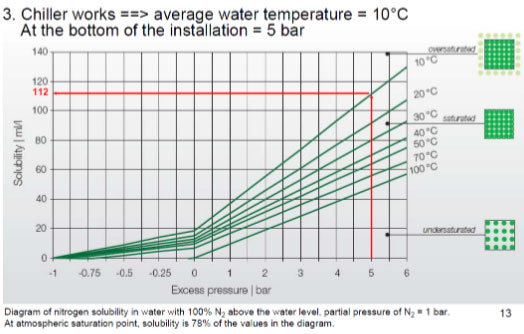
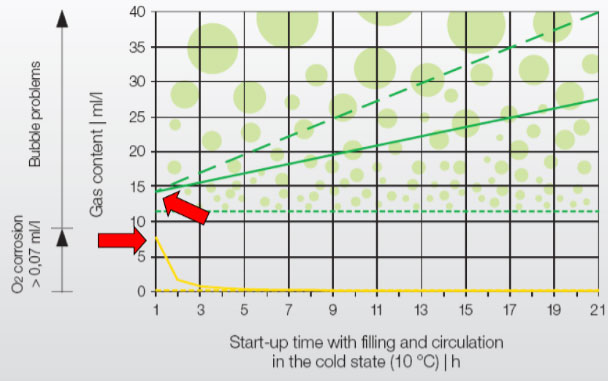
The rate of nitrogen in a dissolved state increases with pressure which exist in the form of free air bubbles at lower pressures. In every piece of equipment that changes pressure to operate, (think pumps, control valves, bends etc.), nitrogen causes havoc with pitting, cavitation, erosion and corrosion.
The Solution:
So what is the solution? Given below are three ways to combat the above.
- Invest wisely in equipment that is sized correctly based on actual system requirements such as:
- Location of installation of the pressurisation units.
- Static height of the system (to calculate the Pf factor and pump head).
- Actual calculated system volume (to calculate the expansion tank water volume).
- Total cooling capacity (To calculate the Pump flow rates).
- System safety valve.
- Install vacuum degassing units and route the water make-up system through this device.
- Install a high-efficiency dirt separator which can separate dirt as small as 5 microns (that is the size of magnetite rust).
While pressurisation and air management equipment are not as glamorous as other equipment like pumps, control valves and FAHUs, they play a vital role in maintaining the health and performance of systems.
At FlowTherm, Leminar Air Conditioning Company, we provide in-depth training on the science behind the correct engineering of pressure and air management systems. In our next chapter, we will address the problem of air diffusion in closed systems.
For more news and developments from the industry, stay tuned to the MEP Times!
Author: Anoop Sequeira
Designation: Certified Energy Manager (CEM) and Sales Manager, Leminar Air Conditioning Company
References:
IMI Pneumatex: Breakthrough Engineering